Product Details
-
Cast iron platform flat series
-
Marble measuring tool
-
3D welding platform
-
Square box/bending plate
-
Series of cast iron flat ruler
-
V-frame series
-
Magnesium aluminum measuring tool
-
Skew instrument series
-
Plug ring gauge series
-
Machine tool pad iron series
-
Machine tool casting series
-
Counterweight iron series
-
Cast iron flooring
-
Ground rail series
-
Special wrench series
-
Other series
-
Machine tool inspection measuring tools
-
Haval Festival series
-
Valve series
-
Casting
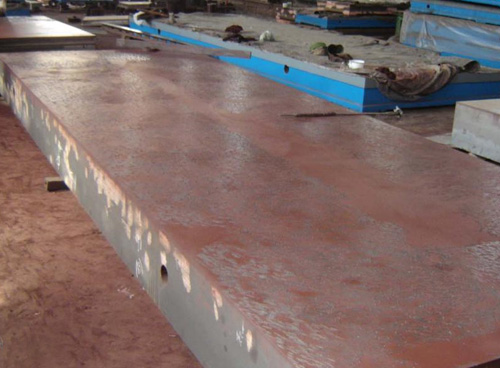
Scraping and grinding of cast iron platform flat plates for maintenance
Requirements for maintenance and scraping of cast iron platform plates:
1.The flatness of the flat working surface should not exceed the specified value.
2.The flatness at the upper edge of the working face may not be calculated at the specified distance,but at this distance,it shall not be higher than the flat working face at any point.
3.The overlap of the flatness of the calibration points for each section of the flat working face should comply with the regulations.
Testing method for scraping and grinding repair of cast iron platform flat plates
1.The number of test points on the tested tablet should comply with the regulations
2.When using the diagonal method for verification,the number of verified sections meets the regulations.
3.Other distribution forms of acceptance points are allowed,but the uncertainty of the calibration method should comply with regulations.
4.Method for calibrating the flatness of a flat working surface using small angle instruments(such as autocollimators and levels)
During the 5 inspections,select the appropriate span of the bridge slab according to the specifications of the inspected slab.Then place the bridge slab at one end of each section of the inspected flat plate,and place a reflector or level on the bridge slab.Move the bridge slab from one end of the flat plate to the other end in a straight line,and read the readings(number of grids)at each position using an autocollimator or level.Every time the bridge deck is moved,it should be connected at the tail.During the movement of the bridge deck,the reflector or level must not have any displacement relative to the bridge deck.
6.Read the readings of the bridge deck at each measuring point on each section using an autocollimator or level(μm)According to the evaluation principles,data processing is carried out to obtain the flatness of the flat working face.
The method of using a template ruler to verify the flatness of a flat working surface
1.For grinding flat plates with dimensions less than 400mm x 400mm,a sample ruler can be compared and verified with a measuring block.The calibration tools used should comply with regulations.
2.When using a template ruler and measuring blocks for calibration,place two measuring blocks of the same size(1 mm or 2 mm)at both ends of the section being inspected on the flat plate.Place the template ruler on the measuring block and use micrometer group measuring blocks to plug the gap between the template ruler and the flat plate at the section being inspected point.The difference between the size of the gauge block group when it is just inserted and the size of the two end gauge block groups is the deviation of the line connecting the inspected point to the two end points.According to the evaluation principles,process the data to obtain the flatness of the flat working face.
Data processing of working face flatness
1.Evaluation based on the diagonal principle:The ideal plane(evaluation benchmark)is the plane that passes through one diagonal of the flat working surface and is parallel to the other diagonal.The flatness of the flat working surface is evaluated based on the difference between the maximum and minimum deviation values of each inspected point on the working surface from the ideal plane.The value should not exceed the specified value,which is considered qualified.If it exceeds the tolerance,it should be evaluated according to the principle of small conditions.
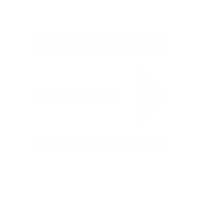
-
The main function of welding platforms
2022-09-08 05:40:39
-
Measures for maintenance and upkeep of the marking platform
2022-09-08 05:39:16
-
Reference plane inspection and application of cast iron platforms
2021-01-24 11:20:22
-
The centralized method and measurement inspection method for installing cast iro
2021-01-20 09:21:17
-
How to Reasonably Design Reinforced Ribs for Cast Iron Platforms
2021-01-19 09:51:22
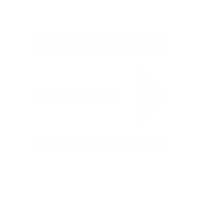
—— E-mail:326673342@qq.com
—— Tel/Fax:+86-0317-8383389
—— Phone:+86-18603177396
—— Address:Linzhuang, Haocun Town, Botou City, Hebei Province