Product Details
-
Cast iron platform flat series
-
Marble measuring tool
-
3D welding platform
-
Square box/bending plate
-
Series of cast iron flat ruler
-
V-frame series
-
Magnesium aluminum measuring tool
-
Skew instrument series
-
Plug ring gauge series
-
Machine tool pad iron series
-
Machine tool casting series
-
Counterweight iron series
-
Cast iron flooring
-
Ground rail series
-
Special wrench series
-
Other series
-
Machine tool inspection measuring tools
-
Haval Festival series
-
Valve series
-
Casting
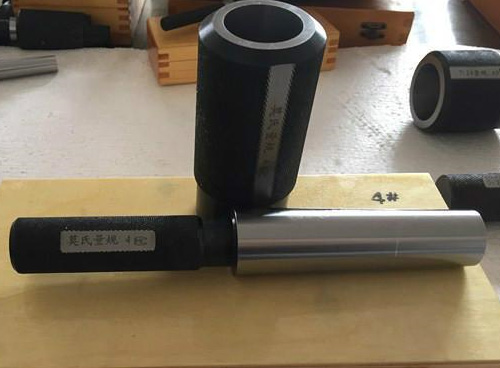
Mohs gauge
Precautions for using Mohs gauges:
1.Before use,it is necessary to carefully inspect.First,check the drawings to see if this gauge matches the required inspection dimensions and tolerances,in order to avoid errors and causing a large amount of scrap.At the same time,it is necessary to check whether the gauge has a qualified calibration mark or other proof.Also,check if there are rust spots,scratches,and burrs on the working surface of the gauge,as these defects can easily cause a decrease in the surface quality of the inspected workpiece,especially for non-ferrous metal workpieces with higher tolerance levels and surface roughness that protrude.Also,check if the connection between the gauge head and the handle is firm.Afterwards,it is necessary to check the inspected parts of the workpiece(especially the inner hole)for defects such as burrs,protrusions,and scratches.
2.Before use,use a clean fine cotton yarn or soft cloth to wipe the working surface of the gauge clean.It is allowed to apply a thin layer of oil on the working surface to reduce wear.
3.When the workpiece clamped on the machine tool is still in operation,it cannot be inspected with a measuring gauge.
4.Do not use a measuring gauge to inspect workpieces with rough or unclean surfaces.
5.The measuring end of the gauge needs to pass through every qualified workpiece,and its measuring surface is often worn out.Therefore,the gauge needs to be regularly calibrated.
6.Use a smooth gauge to inspect the workpiece.If there is a dispute,the following size gauges should be used for inspection;
Usage of Mohs gauge:
The use of gauges to inspect workpieces usually includes the go stop method,coloring method,light gap method,and indicator method.
1.Go/no go method:Use the go and no go ends of the gauge to control the size of the workpiece,so that it does not exceed the tolerance zone.When measuring the aperture,if the through end of the smooth plug gauge passes but the stop end does not,then the aperture is qualified.The gauge used for inspection using the go/no go method is also a weighing gauge(Figure 1).Common gauges include thread plug gauge,thread ring gauge,and caliper gauge.
2.Coloring method:Apply a thin layer of appropriate pigment(such as Prussian blue or red lead powder)on the working surface of the gauge,and then use the gauge surface to blend with the measured surface.The size and uneven distribution of the coloring area on the tested surface indicate its error.For example,using a cone gauge to inspect the taper hole of the machine tool spindle and using a ruler to inspect the straightness of the machine tool guide rail.
3.Light gap method:Make the measured surface in contact with the measuring surface of the gauge,and place a light source behind or use natural light.When the gap is small enough,the optical diffraction phenomenon causes the transmitted light to become colored light,and when the gap is 0.5 microns,the transmitted light can still be seen.The gap size can be determined based on the color of the transmitted light.The size of the gap and the degree of unevenness represent the magnitude of the measured size,shape,or position error,for example,using a ruler to check straightness,using an angle ruler and a flat plate to check perpendicularity(Figure 2),etc.
4.Indicator method:Comparing the accurate geometric shape of a gauge with the measured geometric shape,and using a dial gauge or micrometer to indicate the error in the measured geometric shape.For example,measuring the straightness of ruler shaped workpieces using flat plates and dial indicators;Measure angles using sine gauges,flat plates,and micrometers.
Maintenance of Mohs gauge:
1.Do not store the working surfaces of two gauges together(such as plug gauges and ring gauges),otherwise the two working surfaces will adhere to each other and be damaged when separated by external forces.
2.After using the gauge,it should be wiped clean with clean cotton yarn or soft cloth,placed in a wooden box,and then stored in a tool cabinet;The sheet gauge can also be hung in the tool cabinet.If the weather is humid or can only be used after a period of time,wipe it clean and apply a layer of acid free Vaseline or rust proof oil.The place where the gauge is kept is dry
3.The gauge needs to be inspected regularly,with a general inspection cycle of 6-12 months.
4.Both frequently used and infrequently used gauges should undergo regular external inspections to check for damage,rust,or deformation.If the gauge starts to rust,it should be soaked in gasoline for a period of time,then carefully wiped clean and coated with rust proof oil.
5.During use,place the gauge in an appropriate place,such as on the countertop of the tool cabinet or on the wooden pad of the stationary part of the machine tool.Do not place it on the tool holder or guide rail of the machine tool to avoid damage.
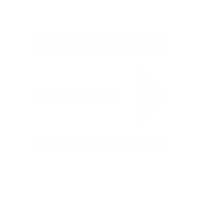
-
The main function of welding platforms
2022-09-08 05:40:39
-
Measures for maintenance and upkeep of the marking platform
2022-09-08 05:39:16
-
Reference plane inspection and application of cast iron platforms
2021-01-24 11:20:22
-
The centralized method and measurement inspection method for installing cast iro
2021-01-20 09:21:17
-
How to Reasonably Design Reinforced Ribs for Cast Iron Platforms
2021-01-19 09:51:22
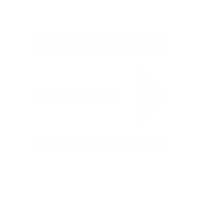
—— E-mail:326673342@qq.com
—— Tel/Fax:+86-0317-8383389
—— Phone:+86-18603177396
—— Address:Linzhuang, Haocun Town, Botou City, Hebei Province