Product Details
-
Cast iron platform flat series
-
Marble measuring tool
-
3D welding platform
-
Square box/bending plate
-
Series of cast iron flat ruler
-
V-frame series
-
Magnesium aluminum measuring tool
-
Skew instrument series
-
Plug ring gauge series
-
Machine tool pad iron series
-
Machine tool casting series
-
Counterweight iron series
-
Cast iron flooring
-
Ground rail series
-
Special wrench series
-
Other series
-
Machine tool inspection measuring tools
-
Haval Festival series
-
Valve series
-
Casting
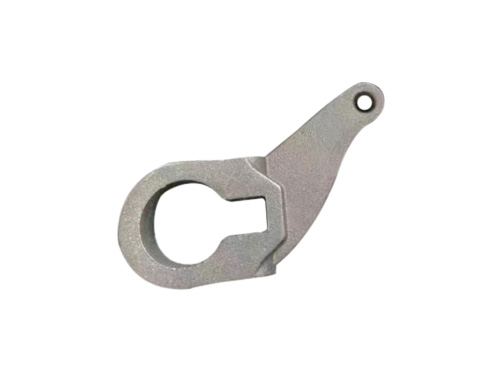
Small castings
In general,there are two reasons for the occurrence of sand sticking defects in castings:a.detachment or cracking of coating,during which metal liquid seeps into the molding sand,easily forming mechanical sand sticking;When the coating selection does not match the metal liquid,and there are small sand particles and dust in the dry sand,chemical bonding sand will form.b.The influence of negative pressure on the flow capacity of molten metal during pouring.The greater the negative pressure,the better the fluidity of the metal liquid,and the easier it is to form sticky sand.
Measures to prevent sand sticking defects:
a.Choose a lost foam coating with high fire resistance,good density,sufficient strength,stable performance,and the ability to firmly bond the pattern;
b.During the styling stage,it is important not to make it too large to prevent damage to the coating layer;
c.According to the material of the casting,the negative pressure is reasonably controlled.The steel casting is 40-59Kpa,the cast iron casting is 26.7-53.3KPa,and the aluminum alloy casting is 0-26.7KPa.
d.During the casting process,the pouring temperature should not be too high.Generally,the mold temperature is 30-50℃higher than that of sand casting under the same conditions.
e.Reduce the gap between molding sand and choose finer raw sand.Generally,28-55 mesh raw sand is used as molding sand for steel and cast iron castings,and 50-100 mesh raw sand is used as molding sand for aluminum castings.
Small castings with sand sticking can be divided into mechanical sand sticking and chemical sand sticking.The essence of mechanical sand sticking is the penetration of metal liquid into the pores between sand grains.This situation is caused by the penetration pressure of metal liquid exceeding the gas back pressure in the voids between sand grains and the additional pressure caused by the surface tension of metal liquid.The metal liquid penetrates into the voids between sand grains.If a layer of dense coating is hung on the outer surface of the foam plastic mold,it can prevent the penetration of metal liquid,Thus,the effect is excellent to prevent mechanical sand sticking in castings.The formation of chemical sand sticking is often caused by the low fire resistance and low melting temperature of the mold material.When high-temperature metal liquid is poured in,it is easy to be melted by the metal liquid,forming defects such as nodules.Therefore,isolating a layer of high fire resistance coating between the metal liquid and the mold material is beneficial for preventing chemical sand sticking.
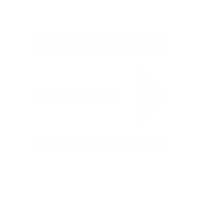
-
The main function of welding platforms
2022-09-08 05:40:39
-
Measures for maintenance and upkeep of the marking platform
2022-09-08 05:39:16
-
Reference plane inspection and application of cast iron platforms
2021-01-24 11:20:22
-
The centralized method and measurement inspection method for installing cast iro
2021-01-20 09:21:17
-
How to Reasonably Design Reinforced Ribs for Cast Iron Platforms
2021-01-19 09:51:22
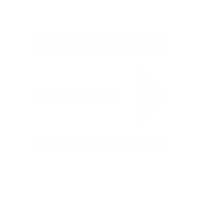
—— E-mail:326673342@qq.com
—— Tel/Fax:+86-0317-8383389
—— Phone:+86-18603177396
—— Address:Linzhuang, Haocun Town, Botou City, Hebei Province