Product Details
-
Cast iron platform flat series
-
Marble measuring tool
-
3D welding platform
-
Square box/bending plate
-
Series of cast iron flat ruler
-
V-frame series
-
Magnesium aluminum measuring tool
-
Skew instrument series
-
Plug ring gauge series
-
Machine tool pad iron series
-
Machine tool casting series
-
Counterweight iron series
-
Cast iron flooring
-
Ground rail series
-
Special wrench series
-
Other series
-
Machine tool inspection measuring tools
-
Haval Festival series
-
Valve series
-
Casting
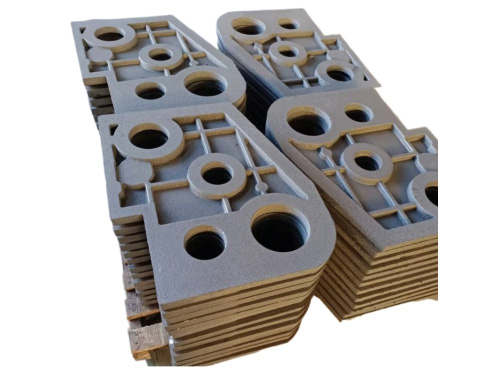
Lost foam casting
Lost foam casting is easy to achieve mechanized automatic assembly line production,with high elasticity.It can produce castings of different alloys,shapes,and sizes on one production line.
The reasons for the occurrence of carbonization defects
a.During the pouring process,the amount of gas generated by the decomposition of the lost foam pattern is too large and urgent,and the exhaust speed of the mold cannot keep up.In addition,the vacuum pump suction is insufficient,which can easily lead to the collapse and collapse of the mold;
b.Flash flow of molten metal is one of the reasons for the occurrence of collapse defects.The so-called flash flow of molten metal refers to the situation where during pouring,some of the molten metal that has already flowed into the position of the lost foam pattern is diverted to other parts under external influence,making the previously replaced position unoccupied by molten metal or metal filling.This type of problem often occurs in situations such as top pouring,large flat surfaces in castings,and one type with multiple patterns;
c.If the buoyancy of the metal liquid is too large,it will make the upper part of the mold sand easy to deform,which may lead to local collapse;In general,a small amount of sand is consumed at the top of the mold,and the negative pressure is not enough,which may cause poor molding or even inability to form the casting;
d.The insufficient fire resistance and high-temperature strength of the coating can easily lead to the collapse of the lost foam casting box.The disappearing mold pattern has a buffering effect on the filling and cooling of the molten metal during the pouring process,while also reducing the erosion of the molten metal on the mold.When the metal liquid replaces the lost foam pattern and fills the mold cavity,the dry sand mainly relies on the support of the coating.When the coating strength is not enough or the fire resistance is not enough,local molds will collapse and collapse,especially above the large internal sprue,which is very easy to collapse.
Prevention and Control Measures for Carbon Increasing Defects in Steel Castings of Lost Foam Casting
The prevention and control of carburization defects in steel castings using lost foam casting can be carried out from the following aspects:
(1)Select low-density mold materials.When using EPS,the density of the pattern is controlled at 0.016~0.025 grams per cubic centimeter.Low carbon mold material EPS(C8H8)is changed to EPMMA(C5H8)to reduce the carbon content of the pattern.Hollow structure patterns and hollow structure pouring systems can also be used.
(2)The appropriate pouring temperature and pouring speed are determined by the opening of the pouring system,which determines the flow direction and speed of the steel liquid;As the pouring temperature increases,the pouring speed also increases,the decomposition of the mold material accelerates,making it difficult to completely gasify,and the amount of liquid phase in the product also increases.At the same time,the gap between the steel liquid and the mold decreases,and the liquid phase decomposition products are often squeezed out of the gap,squeezing between the coating and the metal industry,causing an increase in the contact surface and carbon concentration,resulting in an increase in the amount of carburization in these areas.
(3)Choose a reasonable pouring process.The design of the casting and pouring process should accelerate the gasification of the mold material,reduce and stagger the contact and reaction time between the liquid and solid phases in its decomposition products,and reduce or avoid carburization of the steel parts.
(4)Improving the breathability of coatings or dry sand molds,the better their breathability,the faster the decomposition products of the mold material escape,thereby reducing the concentration of decomposition products and contact time in the gap between the steel liquid and the mold.
(5)Add additives(decarburization agents)to the pattern to prevent carburization of steel castings.
(6)Adopting precision molding to meet the casting process.
(7)Use anti-seepage carbon coating.
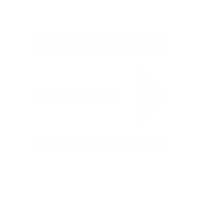
-
The main function of welding platforms
2022-09-08 05:40:39
-
Measures for maintenance and upkeep of the marking platform
2022-09-08 05:39:16
-
Reference plane inspection and application of cast iron platforms
2021-01-24 11:20:22
-
The centralized method and measurement inspection method for installing cast iro
2021-01-20 09:21:17
-
How to Reasonably Design Reinforced Ribs for Cast Iron Platforms
2021-01-19 09:51:22
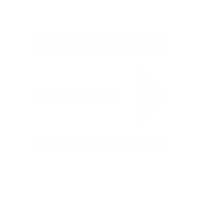
—— E-mail:326673342@qq.com
—— Tel/Fax:+86-0317-8383389
—— Phone:+86-18603177396
—— Address:Linzhuang, Haocun Town, Botou City, Hebei Province