News detail
Technical viewpoints on fine sand and thin coating in lost foam casting of cast
Author:Baichang Machinery Time:2018-12-21 21:38:54 click185
A meticulously crafted manufacturing process
Looking at the shortcomings of forging,they are nothing more than porosity,slag inclusion,and shrinkage.
The crux of this lies in the involvement of the atmosphere and the formation of sand cores.Therefore,vacuum forging and non sand core forging methods have become decisive plans,which has cultivated the vacuum dissipation die forging of cast iron platforms.
Special emphasis is placed on the use of vacuum,with the aim of improving the characteristics of vacuum and achieving remarkable results in forging.
1)Defects of porosity in low cast iron platform castings
2)Extract slag inclusions from castings
3)Enhancing the filling ability of cast iron flat plate casting
4)The dissipation of temperature during low temperature casting is the benefit obtained from vacuum dissipation forging method,but the crux lies in the permeability and slag permeability of the coating.In recent years,the concept of slag permeability has been proposed in the domestic vacuum dissipation die forging industry,aiming to improve various achievements encountered in the domestic market by proposing the application of fine sand and thin coating techniques.The concepts of fine sand and thin coatings are not practical,but examples of their past applications.The specification of fine sand is between 80-100 mesh,and the thickness of thin coating is between 0.3-0.6mm.Fine sand is used as molding sand and thin coating in the aluminum alloy vacuum dissipation die forging technique.When flipping the box after forging,similar tar materials can be found on the outside of the molding sand.The material is the gelatinous material that occurs when the white mold fails to vaporize due to the aluminum alloy casting temperature.Vacuum suction and slag permeable coating are used to extract the gelatinous material from the mold cavity and suck it into the molding sand,Improving the porosity and slag inclusion performance of aluminum alloy castings,this is a resume obtained from practicing vacuum dissipation die forging techniques for aluminum casting.
The application of vacuum dissipation die forging in cast iron and steel also has similar characteristics.Therefore,the concept of vacuum dissipation die forging using fine sand and thin coating is proposed,and its advantages are as follows:
1)High breathability,effectively improving pore performance
2)High slag permeability,effective suction of carbon slag,low drop disadvantage
3)Fine sand has high fluidity,improves the casting quality of the platform,and lowers the sand deposition performance.
4)The amount of paint used is small,resulting in low paint costs.
5)The paint is dull and low in cost.
6)Improved the phenomenon of back spraying during casting,preventing the phenomenon of white mold wetting caused by back spraying.
7)The gravitational acceleration of fine sand is relatively small,and when the appearance is low,it can deal with the destructive force of the white mold and prevent its deformation.
8)When the cast iron platform(welding platform)is coated with slurry,the coating should be light and floating to prevent the white mold from deforming or damaging due to the coating being too thick.On the other hand,many dissipation mold forging factories in the world use heavy coatings,coarse sand,and even bead sized sand in vacuum dissipation mold forging.The thicker the sand,the stronger the coating strength to prevent sand sticking.The stronger the coating strength,the thicker the thickness will be.The thicker the coating,the worse the breathability,and the larger the sand particles will be.This vicious cycle continues,causing the white mold to easily crack when stained with slurry,The number of times the slurry is soaked increases,and when the slurry is soaked,the water once again penetrates into the white mold,causing complete and dry casting reverse spraying.The coating thickness is large,the air permeability is poor,and the fluidity is poor,resulting in defects such as porosity and slag holes in the casting.In order to improve the fluidity,the pouring temperature is increased and the size of the casting port is increased,which leads to cost improvement.The effect is that all dissipation mold forging factories have high costs and poor management.Even the ceramic shell made by coating is the same as the lost wax forging,and then the white mold is burned before casting,completely violating the meaning of vacuum dissipation die forging.
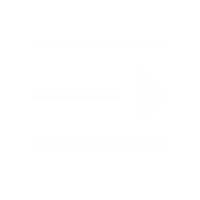
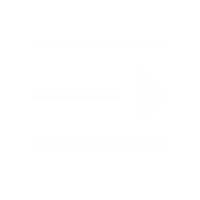
—— E-mail:326673342@qq.com
—— Tel/Fax:+86-0317-8383389
—— Phone:+86-18603177396
—— Address:Linzhuang, Haocun Town, Botou City, Hebei Province