News detail
What are the requirements for melting molten iron on a three-dimensional flexibl
Author:Baichang Machinery Time:2018-12-19 21:38:31 click191
In the family of forged alloys,the growth of forged alloys on three-dimensional flexible welding platforms depends on their superior performance and restraint.Compared to cast steel and non-ferrous alloys,cast iron has better forging performance and can easily produce platform castings with complex shapes and average wall thickness,with fewer forging defects.Therefore,the product of molten iron has a wide range of practical applications.In addition,graphite cast iron has some inherent characteristics such as friction reduction,shock absorption,machinability,fatigue fracture,etc.
In the competition for materials,improving the specific strength of cast iron,increasing its strength and toughness,eliminating internal defects,dealing with increased casting weight,extending service life,and frugal materials are extremely tight.In order to ensure the reliability and stability of the cast iron function of the three-dimensional flexible welding platform,the first quality of molten iron is required.
1、The intrinsic quality of molten iron in three-dimensional flexible welding platforms(cast iron platforms)
The quality of molten iron includes temperature,identity and identity accuracy,element content,number of non-metallic inclusions,gas solubility,and workability outside the furnace.
The quality control of molten iron can be divided into three key points:smelting,pre furnace disposal,and filtration.The following is a brief description of Botou Baichang
2、Melting of 3D flexible welding platform
1.The cupola needs to reach a new level
Obtaining low-temperature molten iron
The process temperature for pouring cast iron parts on the cast iron platform is not high,and most of the cast iron is between 1260℃and 1400℃.But from the concept of obtaining molten iron,there should be a higher melting temperature.Low temperature melting ensures a high tapping temperature,reduces the burning loss of Fe,Si,and Mn,maintains stable furnace conditions,and minimizes chemical fluctuations.For example,in a developed furnace,the turbulence of C can be controlled within±0.05%,and the turbulence of Si can be controlled within±0.1%.Low temperature melting reduces the S,O,H,N,and inclusions in the molten iron,which weakens the poor heritability of the furnace charge.
There are three ways to obtain low-temperature molten iron from a three-dimensional flexible welding platform for a cupola:first,a good furnace type,such as two rows of large spacing,cool air,and coke with a solid carbon content of 85%or more,and the tapping temperature can be above 1480℃.The second method is oxygen rich air supply,which is lightweight and quick to adjust temperature in real-time.However,it is limited by the premise of oxygen supply and has significant limitations.The third is hot air supply,and the temperature of the assembled hot air varies from 150℃to 600℃,making it suitable for use in factories with longer opening hours.
Most forging factories in our country have a relatively small scope of labor,so during this period,"Method One"will be the main step.Cool wind homework,the low heat utilization rate of the cupola,from the perspective of sustainable growth strategy,hot wind cupola conforms to the national policy of energy conservation,and can jointly handle environmental purification,satisfying social and ecological requirements.With the growth of the global economic integration process,the forging industry is bound to restructure,annex,expand its scope,fulfill intensive labor,and gradually expand its utilization scope.The two issues to consider whether to adopt hot air or not are whether there is sufficient time for continuous homework,and the number of one-time investments and the payback period of investments.
②Stable furnace size
Low quality lining materials can have a series of adverse effects:purifying molten iron with corrosive substances in the lining;Corrosives transform the physical and chemical properties of slag,thereby affecting the smooth operation and desulfurization consequences of the furnace;The expansion of the furnace damages the stability of the smelting process.After a long period of time,the temperature of the molten iron will decrease,the burning loss will increase,and the molten iron will oxidize in the later stage.
2.Utilize intermediate frequency sensing furnace
In recent years,Baichang has visited the Yangtze River Delta,the Pearl River Delta and Jiaodong region,and many factories have invented and adopted the feeling furnace or the cupola.The feeling of furnace iron liquid is often based on the supply conditions specified by foreign buyers and domestic host factories.
In the 1990s,the third-generation transistor module intermediate frequency furnace replaced the traditional thyristor intermediate frequency furnace.The characteristics of this type of furnace are energy-saving,melting,quick heating,easy operation,reliable operation,no disturbance to the power grid,and high power output.
The variable frequency intermediate frequency furnace can meet the different process requirements during the different melting stages.When melting the material,use a higher frequency to complete rapid melting;When increasing carbon,switch to a lower frequency,increase the stirring force of the molten iron,accelerate the carbon increase process,and thus achieve the goal of shortening time and saving electricity.Some furnaces can actively adjust their power according to the difference in liquid level height.The recently launched wide furnace body felt furnace from overseas can achieve indirect loading of large materials.
3.Trace elements in pig iron of three-dimensional flexible welding platform cannot be ignored
Normally,pig iron is only defined as Si,Mn,P,and S when it leaves the factory,and the amount of C and trace elements are left unchecked according to the ore source,without testing,and the background code is unclear.The trace elements in pig iron in China include Cu,Cr,Mo,V,Ni,Ti,Sn,Al,Pb,Bi,Zn,As,Sb,etc.Among them,Cu,Cr,Mo,V,Ni have no negative effects.Al is considered neutral,while As,Zn,Pb,Ti,Sb,Bi,and Sn are sensitive elements.Values below these values are not beneficial,while crossing them has drawbacks.
4.Feeling carbon increase in the furnace
If the furnace uses scrap steel as the main material,adding carbon and decomposing cast iron in the furnace can obtain the usual polluted iron liquid like steel.Due to the lack of inheritance and fertility of small graphite in pig iron,the graphite in cast iron structure has the characteristics of being small and evenly distributed.The spheroidization rate of ductile iron is high,and low-carbon gray iron is easy to obtain A-type graphite and pearlite matrix,and the sensitivity of wall thickness is reduced.Due to the low phosphorus content,it reduces the disadvantage of loosening and leakage in the mobilization mechanism.
The commonly used carbon enhancing agents include graphite based carbon enhancing agents(electrode blocks or natural graphite,graphite like)and carbon based carbon enhancing agents(such as metallurgical coke).The electrode texture is pure,with an ash content of less than 0.5%,and only 0.1%of S and N content is required.When selecting natural graphite and carbon based carburizing agents,special attention should be paid to their ash content,S and N content,and moisture should be avoided.The absorption rate of carburizing agent is 65-70%when the bottom of the furnace is added(loaded),and 75-80%when the mirror is added.At the horizontal level,the recovery rate increases with the improvement of disposal temperature,but after exceeding the equilibrium temperature,the recovery rate decreases due to the carbon consumption of the sector in the reaction(SiO2)+2C=[Si]+2CO.The melting point of carbon is 3727℃,and carbon atoms enter the molten iron through process melting and dispersion methods.The carbonization process is controlled by the particle size of the carburizing agent and the stirring of the melt.
Disposal before the third furnace
1.Desulfurization
Desulfurization of molten iron can reduce the amount of spheroidizing agent and the number of sulfide inclusions in castings.Developed ductile iron almost all adopt desulfurization technology,with a request for S≤0.01%after desulfurization.In China,the target level is S≤0.02%,and tin and regular firewood can reach S≤0.015%.
The Na2CO3 penetration method at the bottom of the package is a lightweight method with low desulfurization rate and unstable consequences.During disposal,the smoke and dust purify the environment,which can be irritating to the throat.In the ductile iron workshop where the scope is to be delivered,it is advisable to place the desulfurizer on the liquid level and use machine stirring method,shaking bag method,or pneumatic stirring method to stop sulfur.The pneumatic method is relatively simple and has low energy consumption,making it popular.The pneumatic desulfurization assembly can be installed downstream of the front furnace to stop continuous desulfurization,or it can be continuously desulfurization in a single package in front of the furnace.
2.Slag removal
The slag removal process can be stopped in the bag or felt inside the furnace.Sprinkle the slag remover(agglomerating agent)on the liquid surface to immediately form a molten layer,which covers and agglomerates the slag.The slag remover undergoes thermal expansion,resulting in many small pores in the molten layer,which plays a role in thermal insulation.
The slag remover is divided into three levels:low,medium,and high.The products produced by simple fracturing and sieving of the original ore belong to the same province.It is no longer favored by forging factories.The mid-range slag remover has made choices for the raw ore and increased the water washing process,which can meet the fundamental requirements of castings and is accepted by most factories.The slag remover at the entrance,the ore dressing source,and the processing process are different from ordinary ones.This product quickly spreads on the liquid surface,covering the entire liquid surface.It can only remove slag with a small amount and does not stick to the furnace lining and pouring ladle.It can be lifted up completely with a stick,making slag cleaning convenient.In the past three years,it has begun to be valued by the domestic industry.
3.Spheroidization
The treatment of spheroidization still relies mainly on the method of penetration inside the package.The selection of spheroidizing agents depends on the furnace,tapping temperature,desulfurization,and the type of ductile iron used.As usual,Mg7~9%and RE3~7%spheroidizing agents are used for cupola iron liquid.It is felt that low Mg(5-6%)and low RE(1.5-2.5%)spheroidizing agents are used for furnace iron liquid,and some factories still use Mg8RE3 spheroidizing agents.According to the JB/T9228-1999 standard,the identity range error of Mg and RE is defined as±1%,and some factory standards have been reduced to±0.5%.There are also clear provisions for Ca,Al,etc.In the quality of spheroidizing agents,attention should be paid to the MgO content,segregation level of identity,and concentration of particle size.Any spheroidizing agent with uneven particle size,abundant powder,and dull luster should not be selected.
In principle,it is only necessary to control the chemical identity and incubation crux of the molten iron,and adopt the above-mentioned spheroidizing agent to produce as cast ductile iron.But some factories also adopt spheroidizing agents for cast ductile iron.As usual,as cast ferrite spheroidizing agents contain Ba and Bi,and as cast pearlite spheroidizing agents contain Ba and Sb.However,for tension crankshaft castings with QT700-2 and above,it is not recommended to use Sb containing spheroidizing agents.In this case,the content of Cu,Mo,etc.should be adjusted through the process to control the matrix.It is pointed out that regardless of whether or not the as cast spheroidizing agent can be adopted,incubation is a crucial issue that cannot be ignored.
4.Pregnancy
Pregnancy is the key to improving the quality of cast iron.After ten years of hard work,China's inoculants have fundamentally completed serialization and commercialization.
5.Alloying
The commonly used alloying elements in cast iron include Si,Mn,Cu,Cr,Mo,Ni,Sn,Sb,V,Ti,P,etc.Si,Mn,Cr,Mo,and P participate in the form of ferroalloys,Cu,Ni,Sb,and Sn participate in the form of metals,and V and Ti participate in the form of ferroalloys or VTi pig iron.The opportunity to participate depends on their melting point,oxidizing ability,and density,whether it is in the back of the furnace(cupola),inside the furnace(felt furnace),or in front of the furnace.In order to facilitate the melting and absorption of high melting point ferroalloys,in addition to reducing particle size,adopting a feverish alloying agent or wire feeding method is an ambitious step.
Four filters
Metal filtration techniques are widely used in developed industries.Practice has proven that the effectiveness of the key components does not depend on the mechanical performance of the test bar,but on the external soundness level of the three-dimensional flexible welding platform casting.Therefore,it is not advisable to seek the perfection of metallographic structure purely.The factories visited all value the final stage of filtering in their products.As usual,small parts adopt fiber filter screen,and large or tight parts adopt honeycomb ceramic filter or foam ceramic filter.
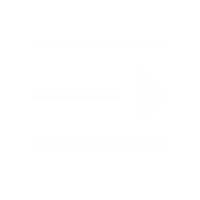
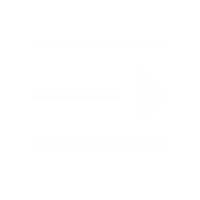
—— E-mail:326673342@qq.com
—— Tel/Fax:+86-0317-8383389
—— Phone:+86-18603177396
—— Address:Linzhuang, Haocun Town, Botou City, Hebei Province