News detail
How to master the smelting of scrap steel when producing cast iron platforms
Author:Baichang Machinery Time:2018-12-09 22:11:07 click122
In the traditional delivery process of cast iron platforms,it is common to use more than 10%carbon scrap steel to stop batching.When using a gray cast iron platform in a cupola or electric furnace for delivery,there are some achievements that should be paid extra attention to during the delivery process after improving the utilization ratio of carbon waste steel.Based on the theory of childbirth,Baichang Skills editor proposed insights:
1.Selection of furnace materials
(1)The scrap steel used in the gray cast iron platform for delivery should be carbon scrap steel.This should not contain elements that hinder graphitization,such as chromium.It should not contain anti spheroidizing alloy elements.The scrap steel should have a block size of around 30%and be in a thick sheet shape,which can be placed flat in the furnace.
(2)Carburizing agent①Excellent coke.The sulfur content should be low,with a block size of 60-80,and high strength.After being burned red,it cannot be easily crushed with just one pound Waste electrode blocks.It should be of good length for easy insertion into molten iron.
(3)Pig iron tension is used to adjust the carbon content of molten iron.I hope to use high carbon and low sulfur pig iron with a wC greater than 4%.It is better to have a slightly higher silicon content in pig iron,and to add less silicon iron to ductile iron for delivery.
(4)Spheroidizing agents and inoculants are used according to traditional processes and are subject to the actual situation of each factory.
2.Melting
Melting process flow:coke block+scrap steel→electrode block→heating→removing coke block and electrode block→sampling and analyzing carbon content→pig iron→returning furnace material→sampling and analyzing Si and Mn→heating→manganese iron+silicon iron→discharging→incubation+spheroidization→pouring.
The precautions during the smelting process are as follows:
(1)The coke block is installed at the bottom of the furnace,with the goal of inventing a longer soaking time for the coke block in molten iron.The amount of coke blocks used is 5%of the scrap steel,Your Excellency.Melt 50%of the scrap steel,sir.Use thick sheets of scrap steel on top of the coke to conceal.It is also possible to replace coke with 60-80 sister's waste electrode blocks and install them at the bottom of the furnace as a carbonizing agent,which has a sulfur content and is not beneficial for high-quality ductile iron.
(2)The tight utilization ratio of scrap steel determines the effectiveness of carbon enhancement.It is advisable for manufacturers of ductile iron to start using this method,with a price of around 30%.After improving the effectiveness of carbon enhancement,the proportion of scrap steel utilization gradually increases.Excessive utilization of scrap steel,if the carbonization effect is not high,will affect the carbon silicon equivalent of the product.
(3)After the scrap steel is melted,it is inserted into the electrode rod,and the temperature inside the furnace is appropriately increased to improve the effectiveness of carbon enhancement.However,if the furnace temperature is too high,it will increase electricity consumption and be detrimental to the furnace lining.
(4)After estimating the carbon content to be high enough,remove the coke block and electrode rod,and take a sample to analyze the carbon content.
(5)Based on the analysis results,calculate the amount of pig iron participation and the utilization amount of return furnace ductile iron.
(6)Based on the silicon content budget,it is decided whether the total amount of molten iron can be supplemented with recycled materials.
(7)After the furnace material is melted,take samples to analyze the content of alloying elements such as Si and Mn.
(8)Properly increase the temperature of the molten iron,supplement the alloy elements according to the analysis results,and participate in ferrosilicon before reaching the furnace temperature.
(9)Melt the ferrosilicon to its molten state and immediately remove it from the furnace.
(10)Spheroidization,incubation,and pouring are carried out according to convention
3.Identity adjustment calculation
As is well known,the mechanical properties of gray cast iron depend heavily on its chemical identity,cooling rate,and heat treatment process.Chemical identity is an internal factor,fundamental,and variable,almost every furnace is different.Therefore,it is not advisable to adopt a"firm proportion delivery"approach to enhance the detection of chemical identity and adjust it vigorously.In chemical identity,carbon equivalent is particularly important.Special attention should be paid to adjusting the carbon equivalent of gray cast iron,which uses scrap steel as a tense furnace material.Due to the difficulty in controlling the carbonization effect and the large fluctuation of carbon equivalent,it is particularly important to use scrap steel as a tight furnace material.
(1)Calculate the participation of pig iron based on the analysis of carbon content.In fact,it is to adjust the carbon equivalent of ductile iron,so that the carbon equivalent of the molten iron composed of pig iron and scrap steel reaches the carbon equivalent required for ductile iron.
Pig iron participation=scrap participation x(carbon content requested for ductile iron-carbon content analyzed)/(carbon content requested for pig iron-carbon content requested for ductile iron)
(2)The calculation of the carbon equivalent of return cast iron is basically abnormal,and the participation is not large.Therefore,after the participation of the return iron,the carbon content of all the molten iron in the furnace is qualified.
The participation of ductile iron in the furnace=total amount of furnace charge-participation of scrap steel-participation of pig iron
(3)The budget formula for silicon content is as follows:
Silicon content≈[(participation of scrap steel+pig iron+return ductile iron)x Silicon content/total amount of furnace charge]x 90%≤allowable silicon content of the original molten iron
When the budgeted silicon content is too high,add less excess return ductile iron and replace it with an equal ratio of 9:1 pig iron and scrap steel to make up for the total amount of furnace charge.
(4)The calculation formula for the participation of ferrosilicon in the scale calculation is as follows:
Silicon iron participation amount=[total amount of furnace charge x(requested silicon content of ductile iron-inoculation and silicon increase amount-spheroidization and silicon increase amount-elucidation silicon content)]/Silicon iron silicon content
(5)Manganese and other alloying elements participate in the calculation formula of the scale as follows:
Alloy iron participation=total amount of furnace charge x(requested alloy content of ductile iron-analysis content)/alloy element content in alloy iron
Technical specifications and requests for cast iron platforms
1)Cast iron flat plates JB/T7974-1999
2)Heat treatment of gray iron castings JB/T7711-1995
3)T-groove dimensions GB/T158-1996
4)Unmarked linear public service scale GB/T1804-2000
5)Quality assessment method for castings JB/T7528-1994
The production of cast iron platforms is divided into three stages:forging,rough machining,and precision machining.The entire process is stopped for secondary tempering treatment,which stops after the forging is completed and stops after the casting rough machining is completed.The tempering treatment follows the GB/T 9439-2010 standard(vibration aging plan can also be adopted).
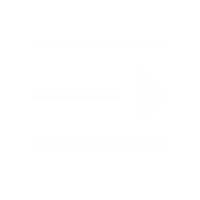
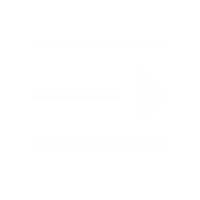
—— E-mail:326673342@qq.com
—— Tel/Fax:+86-0317-8383389
—— Phone:+86-18603177396
—— Address:Linzhuang, Haocun Town, Botou City, Hebei Province