News detail
Precision machining and testing methods for cast iron platforms
Author:Baichang Machinery Time:2020-12-10 22:31:00 click179
When scraping and grinding cast iron platforms,master the three stages of rough scraping,medium scraping,and fine scraping.Some workers,due to their eagerness to achieve results,waste their work time by scraping first and then fine when they shouldn't have scraped.This is mainly because they are eager to add points but do not pay attention to flatness.The surface quality of the scraping process for cast iron plates is that there are no less than 20 contact points on any 25x25mm plane for the plate,and no less than 12 contact points on any 25x25mm plane for the secondary plate.
Scraping process of cast iron plates;
1.Fine scraping is the process of removing high points after rough scraping,characterized by the use of a short scraping method(with a knife mark of about 6mm wide and 5-10mm long),which allows for quick dispersion of research points.Scraping should be done in a certain direction.After scraping once,scrape again at 45 or 60 degrees.When the average grinding point is every 252510-14 points,scraping can be completed.
2.Fine scraping is carried out on the basis of fine scraping.Use a small scraper or a scraper with a curved arc.The width of the knife mark is about 4mm,with an average polishing point of every 252520-25 points,used for scraping and inspecting the contact surface of the cutting tool,guide rail,and tight knife.
Precautions for scraping cast iron plates:
1.Fine scraping will not affect the size of the cast iron sheet,but is only for the sake of the appearance accuracy of the sheet.Special attention should be paid to the sharp lubrication of the cutting edge,forming a 5-angle with the sheet.
2.The knife mark should be small,about 3mm wide and 6mm long.Each knife should be at one point.First,drop the knife in front of the tip and press down firmly at the center of the tip to distribute the bonus.Small black spots can be hidden without scraping,and small bright spots can be gently scraped open.Such a large scratch will turn into a small one,and the middle scratch will have a bonus.The original small scratches will become larger,and areas without scratches will also appear.
3.Pay attention to temperature changes during fine scraping.If the heat treatment of cast iron sheet is excellent,the room temperature change is not significant,and the cast iron sheet is not easily deformed.But if exposed directly to the sun at a certain location on the platform or near a heat source such as a furnace in summer,the cast iron plate will deform.
When the cast iron platform is ground against each other,the stress on the bottom support points(three legs)often leads to the deformation of the flat plate due to the influence of its own stiffness and components.
At the end of fine scraping,there are 26-31 scraping points per 26 square millimeters of cast iron plate,with a bearing area of about 22%and a flatness of every 200 millimeters,with an error not exceeding 0.0038 millimeters
6.The raw material for cast iron flat plates is cast iron HT200-300,and the working surface hardness is HB170-240.Through two manual treatments(600-700 manual annealing and natural aging),the accuracy of the T-shaped groove iron is stable and good.
The fine scraping of cast iron sheets is a crucial process in the production of finished sheets,making it a crucial operation.Scraping is the process of improving the quality and accuracy of cast iron plates without affecting other parameters.Therefore,the fine scraping operation directly affects the quality of the cast iron plate.The process and verification method for cast iron plates are the same.Scraping cast iron plates is a very important task for accuracy.If the fine scraping is not good,it will directly affect the accuracy and price of the cast iron plate.
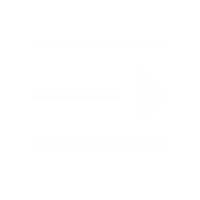
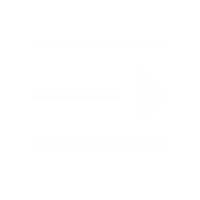
—— E-mail:326673342@qq.com
—— Tel/Fax:+86-0317-8383389
—— Phone:+86-18603177396
—— Address:Linzhuang, Haocun Town, Botou City, Hebei Province